5 Common Trailer Issues That Aluminum Welding Can Fix
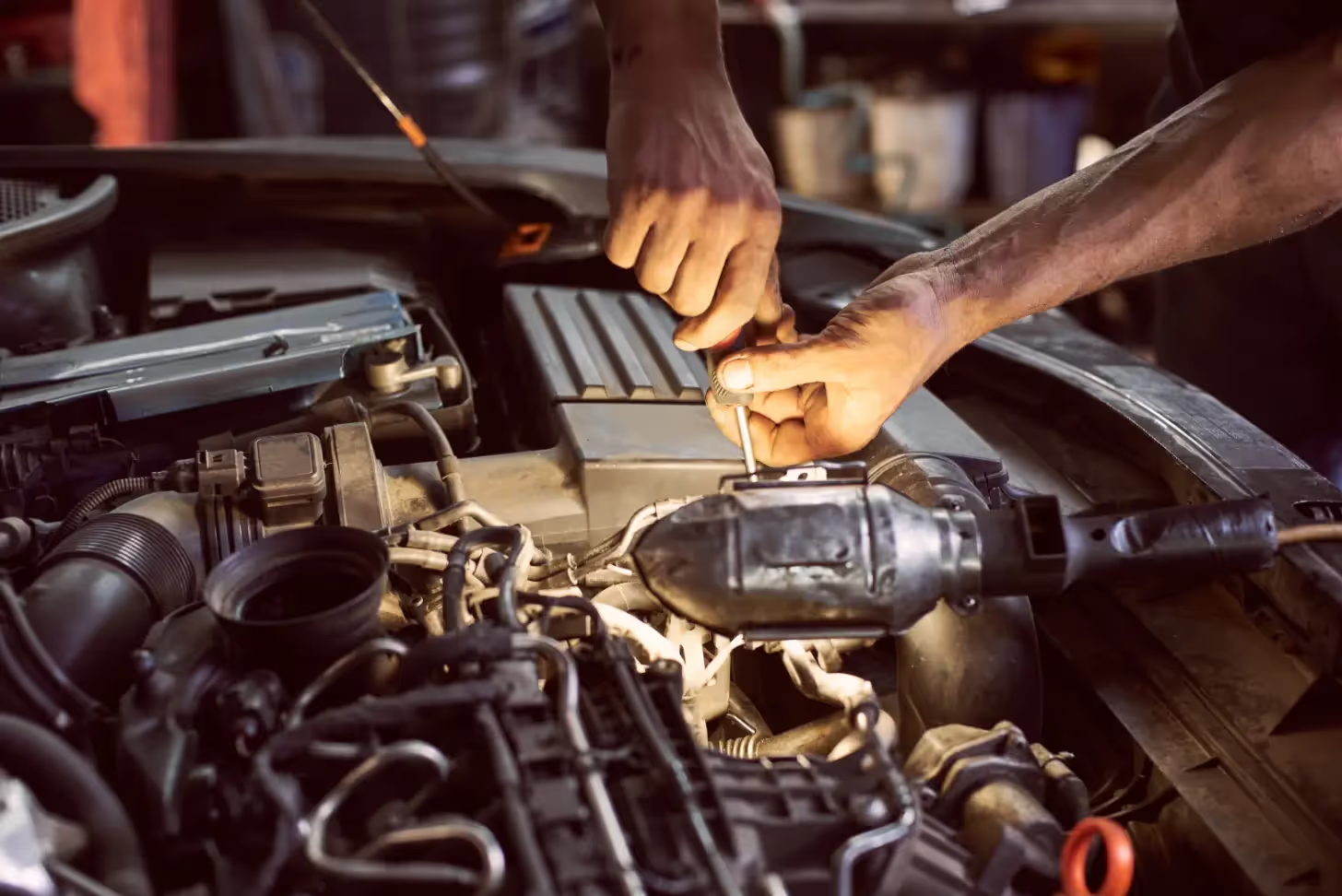
When it comes to heavy-duty trailers, wear and tear are unavoidable. Whether it's corrosion, structural damage, or fatigue from countless miles on the road, trailers can face a host of problems. The good news? Many of these issues can be addressed with aluminum welding.
This technique is a game-changer in heavy-duty trailer repair, offering durable, lightweight, and corrosion-resistant fixes. Let's explore the five most common trailer problems that aluminum welding can solve and why it's the go-to solution for your rig.
1. Cracked or Damaged Trailer Frames
Your trailer’s frame is its backbone, bearing the weight of your load and enduring constant stress. Over time, repeated exposure to heavy loads, rough roads, and weather can lead to cracks or structural weakening in the frame. Ignoring these cracks is like playing a dangerous game of Jenga with your trailer.
How Aluminum Welding Helps
Aluminum welding can seamlessly repair cracks or reinforce weakened areas without adding significant weight to the frame. Skilled welders use techniques that restore the frame's integrity while maintaining its lightweight properties, which is critical for maintaining your trailer’s performance and fuel efficiency.
2. Broken or Bent Support Beams
Support beams distribute weight evenly across the frame. When these beams are bent or broken, you risk uneven weight distribution, compromising safety and leading to further damage.
How Aluminum Welding Helps
With precision welding, damaged beams can be reshaped or replaced entirely. Aluminum welding ensures that new or repaired beams are as intense as the original design, restoring your trailer’s capacity to handle heavy loads.
3. Corroded Trailer Floors and Panels
Trailers are constantly exposed to the elements—rain, snow, road salt, and grime. Over time, corrosion eats away at floors and side panels, leaving your trailer vulnerable to structural issues and leaks.
Why Aluminum Is Ideal for Repairs
Unlike steel, aluminum is naturally resistant to rust. Welding aluminum panels or floors repairs existing corrosion and adds a layer of durability for future protection. Plus, aluminum’s lightweight nature means you’re not adding unnecessary bulk to your trailer.
4. Worn-Out Ramps and Tailgates
Loading and unloading heavy equipment or cargo can take a toll on your trailer’s ramps and tailgates. Over time, stress points can crack or weaken, making them unsafe to use.
How Aluminum Welding Fixes It
Aluminum welding can repair cracks, strengthen stress points, or even replace entire sections of the ramp or tailgate. The result? Ramps and gates that are as sturdy as new ensure safety for operators and cargo.
5. Damage to the Trailer's Roof or Sidewalls
The roof and sidewalls of your trailer endure plenty—impact damage, weather exposure, and general wear and tear. Holes, cracks, or dents can lead to leaks, reduce aerodynamics, and even cause cargo damage.
Why Welding Works
Aluminum welding can seal cracks and restore the roof and walls to their original condition. The lightweight, seamless finish ensures the repair doesn’t compromise the trailer’s overall performance or appearance. This method is beneficial for maintaining a weatherproof seal and keeping your cargo dry and safe.
The Advantages of Aluminum Welding
So, why is aluminum welding the ultimate repair method for trailers? Here are some key benefits:
- Lightweight Strength: Aluminum is both strong and lightweight, making it perfect for heavy-duty applications.
- Corrosion Resistance: Repairs made with aluminum last longer because the material naturally resists rust and corrosion.
- Cost Efficiency: Aluminum welding is often more affordable than full-part replacements, saving you time and money.
- Sustainability: Welding allows for targeted repairs, reducing waste and environmental impact.
How to Spot the Need for Aluminum Welding Repairs
Be proactive about inspecting your trailer for these common warning signs:
- Visible cracks or bends in the frame or beams.
- Rust spots or corrosion on floors and panels.
- Weak or wobbly ramps and tailgates.
- Holes or leaks in the roof or sidewalls.
Addressing these issues early can prevent small problems from escalating into major repairs.
Trust the Experts in Trailer Repairs
Aluminum welding requires a skilled hand and the right tools to achieve durable and reliable results. At Bluegrass Diesel Repair in Grayson, KY, we understand the demands of heavy-duty trailers and are equipped to handle even the toughest repairs.
Our team provides cutting-edge aluminum welding services that cover everything from frame cracks to corroded panels to get your trailer back on the road quickly and safely.
Conclusion
Your trailer works hard for you, so don’t let damage or wear compromise its performance. From cracked frames to corroded floors, aluminum welding is a versatile and efficient solution for many common trailer issues. By addressing these problems promptly, you can extend the life of your trailer, improve safety, and save on costly repairs down the line.
Ready to fix your trailer issues? Don’t wait—contact the experts today and keep your rig rolling strong.